PACHINKO

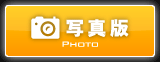
- 1 Pressing
- 2 Nailing and pinwheel mounting
- 3 Nail image inspection and ball action inspection
- 4 Component mounting and front component image inspection.
- 5 Mounting parts to the back side face
- 6 Board inspection
- 7 Board assembly and finished product inspections
- 8 Shipment
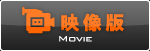
Pachinko machine manufacturing process
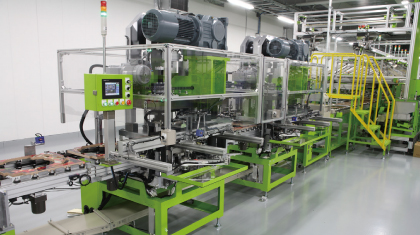
Boards, on which the cells have been mounted and router processing has been performed by a partner company, are temporarily stored in our temperature- and humidity-controlled warehouse.
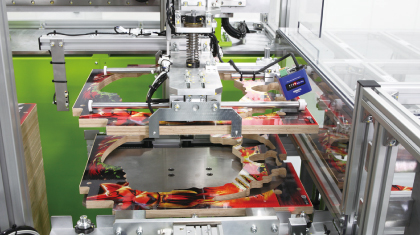
The board is automatically transported to the gauge pressing machine where pressing is performed to instantaneously create component holes and gauge holes.
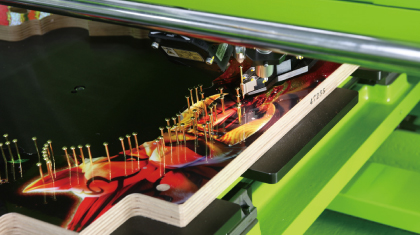
Nailing is performed quietly, with one board being completed in about one and a half minutes.
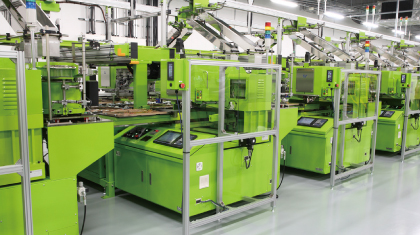
The pinwheel mounter is also fully automatically performed.
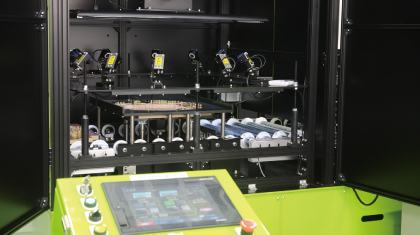
Any irregular height or bending of the nails is never overlooked by the image inspection.
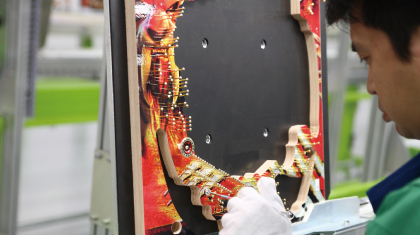
The final check is done manually! A dedicated jig is used for this step.
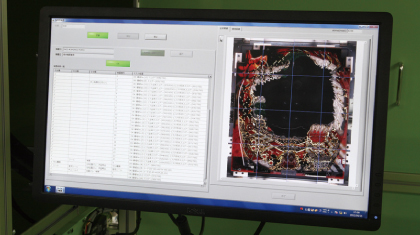
The components to be mounted are all managed based on their QR codes, and are automatically transported to the individual processes. Almost all the mounted components are secured uniformly with an automatic screw tightener.
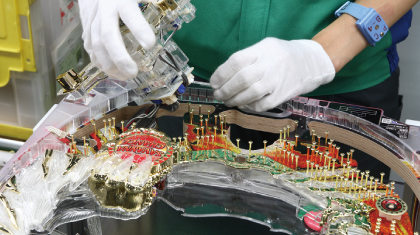
The mounting of the components is inspected with a front component image inspection instrument.
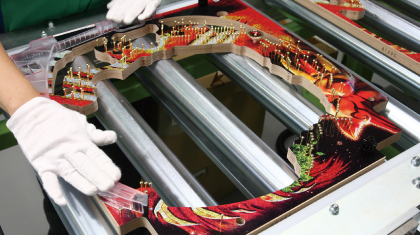
Operation errors that occur during operation, such as missing and damaged screws, are eliminated, thus ensuring stable quality.
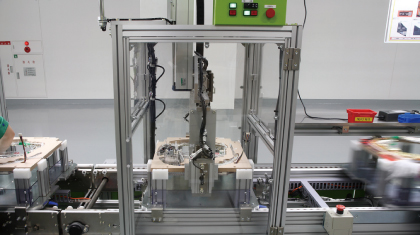
A turnover machine turns over the board so that the back side faces upwards, and then the parts such as the LCD and main PWB are mounted.
Needless to say, all screws are tightened automatically.
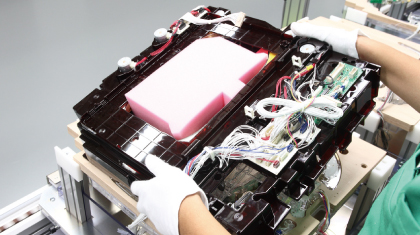
Not a single routing error is permitted, not to mention harness connection errors.
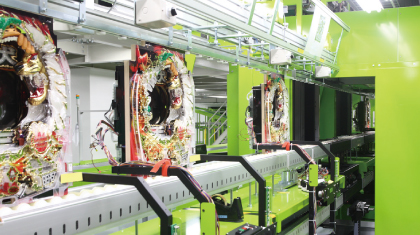
The board to which the parts have been mounted is automatically transported to the inspection process line.
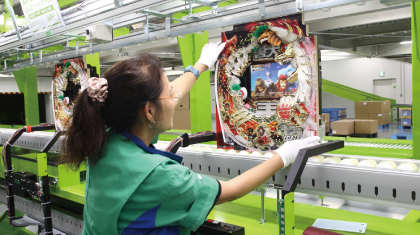
In addition to the inspection by the board image inspection instrument, final confirmation is performed with the human eye, at which point the board is finished.
The latest image inspection instrument helps improve the quality of the visual inspection and allows an inspection to be completed in a short time.
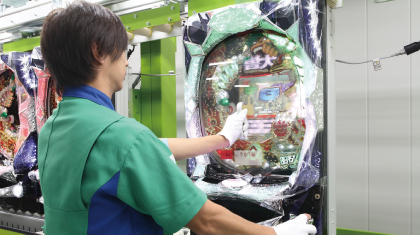
Outer frames including launchers are assembled by partner companies, and delivered efficiently according to the production plan.
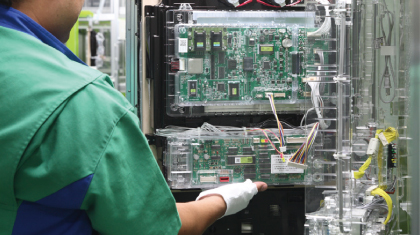
An outer frame is combined with a finished board, after which the assembly undergoes several inspections, such as checks of "each display unit", "each switch", "operating sounds", the "generation of prizes and dispensing of balls", the "launching of balls", and "appearance". Finally, it becomes a complete "pachinko machine".
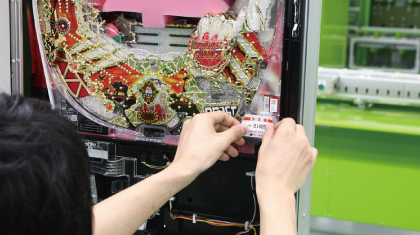
Once its delivery point is determined, a pachinko machine has certificate issued by NIKKOSO-applied, and its shipment destination and date of manufacture are placed under uniform management.
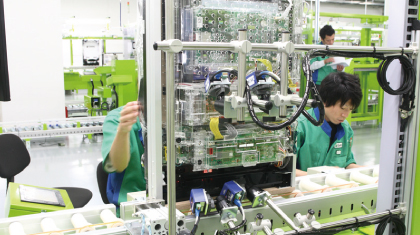
Thorough history management is achieved with a system that makes it possible to instantaneously identify when and where the delivered product was manufactured, by registering links to the QR codes applied to the main PWB, each unit, each part, and so on.
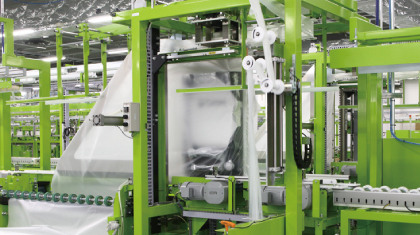
The pachinko machine has a shipping label applied, and is then sent to a distribution center and waits to be opened.
* QR Code is a registered trademark of DENSO WAVE INCORPORATED.